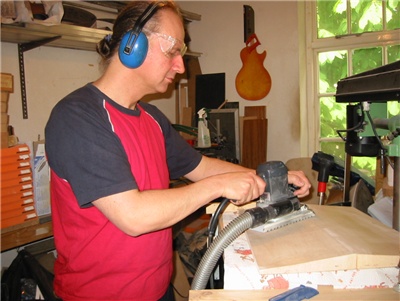
I want a well domed belly on this hand-carved back. So sanding is the only way to keep the thickness under control. I'm not going for 'speed' (I've waited 52yrs........... so what's a little longer) & besides it's a kick watching the grain gradually appear. The actual shape's carved using an assortment of gadgets, most of it's with a 'violin-makers' plane............ but that's later.
Incidentally, I'd like to take this opportunity to thank, "Boulty-Boy's Intrepid Tripod Photomust Amalgamated" for his digital-photo dramatization of this unfolding guitar-making project. His patient, saintly ways have even rubbed of on the leaves, not only are they wonderfully green, but they've even stopped waving as if, posing.
Marvelous mate.......... the kettle's on.